С газом. Без газа. История применения газогенераторов
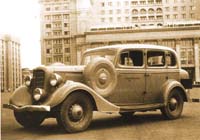
В
Очевидно, что основными потребителями выступали тесно связанные по ряду направлений деятельности лесная промышленность,
Поскольку упомянутые выше виды твердого топлива не могли быть непосредственно использованы в двигателях внутреннего сгорания, то предварительно требовалось перевести их в пригодное к употреблению газообразное состояние в газогенераторных установках, или, по иному, газогенераторах.
Газогенераторы разделялись на стационарные, судовые (малоразмерные суда с газогенераторами — газоходы), мотовозные, «для подвижных машин» (например — экскаваторы), автотракторные.
Автотракторные газогенераторы должны были обладать минимальными габаритами и массой. Переменный режим работы автотракторного двигателя требовал от генератора гибкой и устойчивой работы на всех режимах. Противоречивые требования создавали определенные трудности в разработке автотракторных газогенераторов.
Пионером в создании отечественных газогенераторных установок традиционно считается работавший в северной столице профессор В. С. Наумов, который в 1923 г. построил установку
Превращение твердого топлива в газообразное основано на сгорании топлива, последующем восстановлении продукта горения — углекислоты в окись углерода и разложении водяных паров на водород и кислород в присутствии раскаленного углерода.
Состав газа резко меняется с изменением влажности топлива. Уменьшение влажности влечет увеличение числа горючих компонентов СО и уменьшает количество СО2. Увеличение влажности способствует увеличению СО2 и уменьшению СО.
Окисление топлива требовало введения окислителя; в то время говорили — «подачи дутья». При подаче воздушного дутья получался «воздушный газ», а при подаче пароводяного дутья — «водяной газ».
Процесс газификации топлива происходил в трех зонах: подсушки и коксования; окисления; восстановления.
Расположение этих зон в газогенераторе зависит от способа ведения процесса газификации.
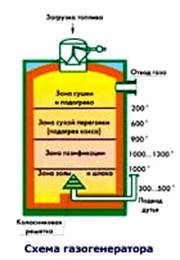
Способ газификации, в свою очередь, зависит от состава твердого топлива, который неодинаков, а потому количество образующейся при газификации смолы, выход золы и, разумеется, газа, различаются. Это не позволило разработать универсальный «многотопливный» газогенератор для массового использования. На автомобилях и тракторах нашли применение газогенераторы трех основных типов, наиболее оптимальные для конкретного вида топлива и конструктивно заметно отличающиеся друг от друга. Выделяют следующие основные способы: прямой, обратный и горизонтальный.
В прямом процессе используются газогенераторы «с противоточным движением газов», «с восходящим движением газов» и «прямого процесса». Все три названия означают одно и то же и равно использовались в книгах и журналах 1930 —
Дутье подается в газогенератор снизу. Окисление топлива происходит в нижней части газогенератора. Отбор газа идет из верхней части.
Топливо, заложенное в верхнюю часть генератора, вначале подсушивается, а затем подвергается сухой перегонке под влиянием высокой температуры в этой части газогенератора (300…400 °С). В результате из топлива выделяется влага Н2О, метан СН4 и углеводороды типа СnНn. Так как отбор газа производится из верхней части газогенератора, то продукты подсушки и сухой перегонки смешиваются с поступающей снизу основной массой газа и уходят из газогенератора без дальнейших изменений.
Оставшаяся после сухой перегонки часть твердого топлива, состоящая в основном из углерода, опускаясь ниже и встречая на своем пути горячий газ (направление движения топлива и газа «противоточное», отсюда и одно из названий), постепенно нагревается до температуры 600…650 °С, вследствие чего углерод приобретает способность вступать в химическое взаимодействие с такими продуктами горения, как углекислота. Углекислота при соприкосновении с раскаленным углеродом переходит в окись углерода СО, причем реакция является эндотермической.
Углерод, не вошедший в химическое соединение с продуктами горения, попадает в нижнюю часть газогенератора, где и будет сгорать, соединяясь с кислородом воздуха, поступающим в газогенератор. Последняя реакция сопровождается выделением тепла, благодаря которому в восстановительной зоне происходит реакция восстановления углекислоты.
В состав газа будут входить окись углерода (СО), углекислота (СО2), метан (СН4), этилен (С2Н4), азот (N2), кислород (О2) и водяные пары (Н2О).
Рассмотрим газогенераторы с прямоточным движением газа (опрокинутый процесс, обращенный процесс). Для содержащих смолы топлив (древесные чурки, торф, бурый уголь) применяют газогенераторы с прямоточным движением газа и топлива. Дутье подается в газогенератор сверху, а газ отводится снизу. Влага топлива и продукты сухой перегонки вместе с газами дутья движутся вниз, нагреваясь, окисляясь и разлагаясь. Опускающееся топливо нагревается горящими продуктами перегонки, и подсушка происходит благодаря теплу, выделяющемуся при окислении топлива. Влага целиком попадает в зону газификации. Газ из газогенераторов обращенного процесса содержит мало углеводородов, повышенное количество водорода и смолы.
Для газификации топлив, не выделяющих смол и с малым количеством золы (до 3…4%), нашли применение газогенераторы с поперечноточным движением газа в топливе (горизонтальный процесс).
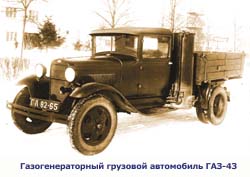
Газогенератор, работающий по горизонтальному процессу, представляет собой цилиндрический бункер, нижняя часть которого, образующая камеру газификации, выполняется из углеродистой листовой стали толщиной 6 — 8 мм. Воздухопроводящая фурма, снабженная воздушным или водяным охлаждением, располагается на некотором расстоянии от днища. Фурма с водяным охлаждением включается в систему охлаждения двигателя или питается от отдельного бачка емкостью в 20…40 л.
Зона газификации локализована в центре камеры в пространстве между фурмой и газоотборной решеткой. Топливо, лежащее на периферии, почти не принимает участия в процессе газификации и выполняет роль тепловой изоляции.
Рассмотрим автомобильные газогенераторы. По соображениям экономического характера в качестве базовых для создания газогенераторных машин использовались коммерческие автомобили, соответствующим образом дооборудованные.
В зависимости от степени приспособленности для работы на газе автомобили условно разделяли на специально построенные, переоборудованные для постоянной работы и приспособленные для временной работы.
Специально построенные в заводских условиях автомобили отличались доработанным двигателем, измененным передаточным числом в главной передаче и иной архитектурой кабины и кузова, а также установкой специальных контрольных приборов и приспособлений.
Автомобили, оборудованные для временной работы на газе, за исключением не всегда рационального размещения газогенератора, не очень отличались от обычных.
Автомобили различались также по типу размещения газогенератора: «рассредоточенно на шасси автомобиля», в виде блочной конструкции и на специальном прицепе. Все три варианта имели как свои достоинства, так и недостатки.
Топливом для газогенераторов служили деревянные чурки или швырок, а также угольные или торфяные брикеты.
Автомобильные бензиновые двигатели при переводе их на генераторный газ существенно теряли в мощности. Если учесть, что газогенераторы обладали значительными собственной массой и габаритами, то становится понятным, почему эксплуатационные параметры газогенераторных автомобилей по сравнению с их «бензиновыми» собратьями сильно снижались.
Как пример могут быть приведены данные по автомобилю
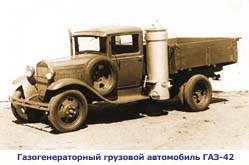
Аналогичной была ситуация с грузовыми автомобилями. Газогенераторный грузовик
Большая часть процессов обслуживания стационарных газогенераторов была автоматизирована, но
Поскольку влажность топлива более 20% сильно понижала температуру горения в зоне окисления, то чурки или швырок требовалось предварительно просушить в специальных сушилках.
Как можно видеть, немногие достоинства газогенераторных автомобилей с лихвой «компенсировались» их многочисленными недостатками.
Вместе с тем, учитывая перспективу сокращения (по мнению оптимистов) или прекращения (по мнению пессимистов) использования производных нефти в качестве топлива, газогенераторные установки вновь могут вернуться.